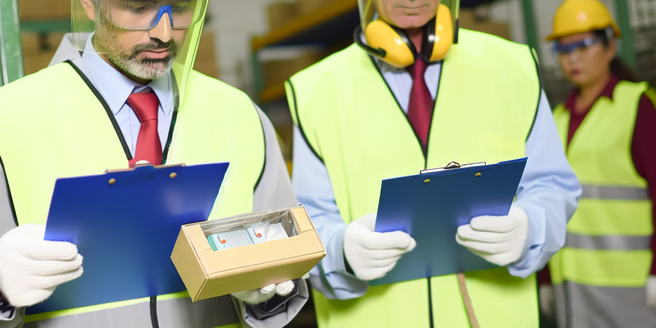
Understanding Product Safety Standards
Product safety standards are baseline requirements designed to ensure the safe utilization of various products or services by the general public, functioning as safeguards to reduce or eliminate risks associated with their use. Regulated by relevant authorities or globally recognized standard bodies such as the International Organization for Standardization (ISO) and the American Society for Testing and Materials (ASTM), these prevent accidents that could potentially arise from product usage. These guidelines, designed and enforced by responsible institutions, aim to protect consumers by substantially reducing the chance of harm due to unsafe or subpar products or services. As an indispensable component of industry, product safety standards mitigate risk, ensure product quality, and protect the health and safety of consumers. Meeting such guidelines is an essential responsibility of authorities and product manufacturers, aligning with their commitment to provide safe and reliable goods.
Importance of Compliance with Safety Standards
Safety compliance is vital in preventing accidents and harm to end users, acting as a shield to protect individuals and businesses from legal issues. Rigorously adhering to safety standards is a proactive strategy against potential injuries and provides businesses a safety net in legal matters.
Compliance also ensures the overall quality of a product or service, playing a significant role in maintaining the credibility of a business. A history of compliance often means higher quality products, establishing a company as trusted and reliable.
Branding can be significantly boosted by adhering to safety regulations; consumers favor businesses that prioritize safety. Emphasizing compliance can result in a positive public perception, fostering trust in customers and influencing their purchasing decisions.
On the flip side, non-compliance can lead to detrimental consequences such as financial penalties and lasting damages to the company’s reputation. Failure to comply not only results in fines that impact financial stability, but it also tarnishes a company’s image, leading to loss in customer confidence and revenue. Rebuilding a damaged reputation demands considerable effort and time, so adhering to safety standards should be viewed as a critical business practice, as non-compliance is too risky.
Common Product Safety Hazards and Risks
Product safety is a critical issue that covers various potential risks including mechanical hazards, fire risks, electrical dangers, exposure to harmful chemicals, radiation effects, and other threats, each presenting unique challenges for ensuring safe consumer use. Mechanical hazards encompass physical harm from equipment’s moving parts, ranging from sharp edges causing cuts to larger components posing crushing or entrapment risks, while fire hazards address threats from combustible products. Improperly insulated wires or equipment lacking auto shut-off features cause electrical hazards, resulting in electric shocks or burns, and chemical hazards result from exposure to toxic or corrosive substances in products. Radiation hazards often involve exposure to harmful radiation from certain appliances. These risks apply across numerous product categories, such as toys posing choking hazards (mechanical) or electronic devices presenting electric shock risks, especially if improperly used or defective. Identifying these hazards is crucial in product design and strategies to reduce risk might include design improvements, safer materials, additional safety features, or clearer usage instructions, all aimed at protecting consumer safety.
Regulatory Bodies and Their Roles in Product Safety
Regulatory agencies and bodies are critical in establishing and enforcing safety standards across diverse markets to guarantee consumer safety and well-being. They work tirelessly to reduce the risk associated with consumer products, always prioritizing consumer protection. They set safety standards, conduct product testing, ensure compliance, and take legal actions like issuing recalls and administering fines for non-compliance.
Prominent examples of these organizations include the US-based Consumer Product Safety Commission (CPSC), and the European Committee for Standardization (CEN), among others. These entities actively monitor consumer goods in the market, regularly inspecting and testing products to ensure they align with defined safety standards. They also promptly initiate enforcement actions, which can include substantial fines for manufacturers or companies failing to meet the safety standards.
Ultimately, the primary goal of these regulatory bodies is to protect consumers from potential harm, highlighting their essential role in consumer safety and public health. They rigorously monitor products, taking necessary actions such as issuing recalls and imposing financial penalties for non-compliance to protect consumers.
Responsibility of Manufacturers in Ensuring Product Safety
Manufacturers are crucial in ensuring the products entering the market adhere to required safety standards through a comprehensive process encompassing design, production, and packaging. It is their responsibility to prioritize safety in product design and production to mitigate any potential harm. Manufacturers are obligated to perform intensive risk assessments on all products, testing each detail to identify and appropriately manage any potential risks. Quality control is also key, with manufacturers needed to apply systematic quality control systems to identify product defects. It’s also incumbent upon them to provide understandable guidelines and instructions about product usage and any possible hazards from misuse. They also have a duty to inform customers of any potential risks through warranty warnings. Ultimately, adhering to safety standards, which includes the design and production of safe products, systematic risk assessments, consistent quality control, and clear usage instructions, is not only necessary for compliance with law but to win and keep customers’ trust.
Consumer Expectations: Rights and Protections
Worldwide, consumers expect products they buy to be safe, a universal belief that prevails across all product types. These safety expectations are a part of consumer rights established by various consumer protection laws across different countries. The laws provide several rights and protections, paramount among which is safety, while also ensuring consumers’ right to clear, honest product information. They guarantee consumers the freedom to choose based on preferences, the right to voice their concerns, and to get just resolutions.
Manufacturers have obligations to honor these rights by ensuring products are developed, tested, and marketed truthfully and safely. Non-compliance can result in legal actions, including lawsuits and fines, severe brand damage, eroded customer trust, and decreased market share. Hence, it’s crucial for manufacturers to respect all laws and obligations tied to consumer rights to ensure product safety.
Legal History: Key Cases on Product Liability Claims
The field of legal history abounds with crucial instances of product liability claims, emerging predominantly when product defects lead to injury or property damage to consumers. Such scenarios necessitate rigorous scrutiny to mitigate harm to users and underline the vital role of product safety in consumer markets. Renowned cases like Liebeck v. McDonald’s Restaurants, globally known as “The Coffee Case,” are stark reminders to corporations and consumers about product safety. Similarly, the Toyota Unintended Acceleration Case emphasizes the tragic consequences of a lack of product safety measures. These cases highlight the dire impact on a business’s reputation and imminent consumer risks, thereby stressing the supreme importance of prioritizing product safety.
How to Handle a Product Liability Claim
Handling a liability claim demands prompt and strategic action. First, it’s vital to contact your insurance firm and your legal adviser for informed guidance. The next step is to rigorously investigate the claim, ensuring to gather evidence, interview witnesses, and documenting your findings. It’s also crucial to fully cooperate with authorities and maintain open communication with all relevant parties, without prematurely admitting liability during the process. An alternative approach in some cases could be offering resolution options to the claimant, like a refund or replacement. This approach should be carefully evaluated per situation. Overall, dealing with a liability claim demands instant response, strategic communication, comprehensive investigation, and considerate decision making.
Preventing Future Liability Issues: Safety Management
Ensuring safety management entails establishing a solid quality control system that spans design to distribution processes to foresee and correct potential risks while saving the business from significant financial loss and damage to its reputation. Regular reviews of safety regulations as part of your business strategy will ensure that your products and services meet minimum legal requirements and win customers’ trust. Developing a schedule to review these standards periodically helps maintain compliance and avoid issues.
Frequent product testing and thorough risk assessments help pinpoint any service-related issues before reaching the customers and mitigating risks. Acknowledging potential risks allows you to manage and limit them, reducing unwanted surprises impacting business and stakeholders.
Promoting a company culture that values safety and quality is essential, with emphasis on providing high-quality products or services to boost your company’s reputation and earn customers’ trust. Regular training and awareness programs promote these values while encouraging employees to participate and reducing unnecessary liability. An environment of responsibility and accountability contributes to the company’s successful operation.
To sum up, it is entirely possible to prevent future liabilities. Proactive safety management, routine updates on safety standards, frequent product testing and risk assessments, and a culture of safety and quality are critical to safeguarding the operations, reputation, and bottom line of any organization.